1.生産計画の平均化
|
---|
生産計画は、お客様の注文に早く応じられることと、生産が平均化していることの両者が満足したものでなければならない。
この両者の満足するためには、お客さまの要望を早く計画に組入れ漸増、漸減していく生産計画を作成していくようにする。
お客様の注文は、一時期に集中してあるものではなく漸増あるいは 漸減の傾向であるから、けっして生産の平均化の考えと矛盾するものではない。
ここでいう平均化は、車種別にとっても、車型別にとってもユニットの種類別にとってもあるいは時間当たりでも、日当りでも月当たりでも平均化しているようにすることを理想としている。
又、生産の遅れが発生した場合は、配車計画の許す限りならし、平均化して挽回するようにしている。
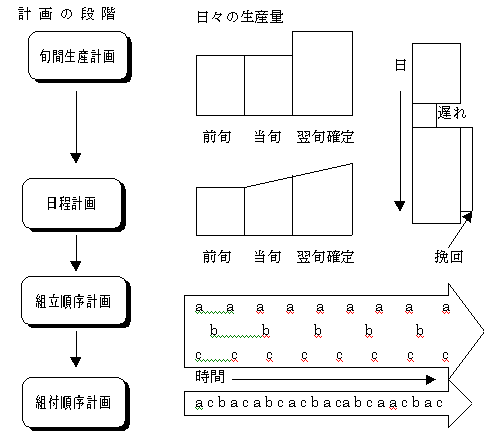
a 日程計画
旬間計画により10日単位で与えられた車型別の生産台数を、車種ごとでも、車型ごとでも、ユニットの種類ごとでも、特殊な仕様ごとでも、毎日の生産台数がてきる限り均等になるように作成する。
(但し、生産単位は大型3台、小型5台ですので、その倍数単位でおこなう)
又、毎日生産するだけの台数がない車型や仕様の車は、一定の間隔をおいて生産するようにする、この条件はよく見落されがちであるが、平均化のためには重要な条件である。
平均化の順序
- イ 組立工場のライン別台数の平均化
- 2本ある組立てラインが、前工程から平均して引取るよう2つのラインの
1日当りの生産台数を同じにする
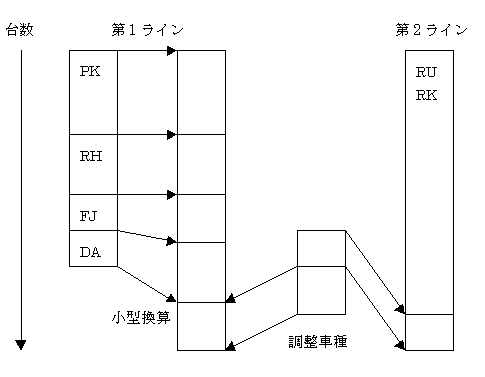
- ロ 車名別の平均化
- ライン別に平均化されると、その枠の中で、車名別に平均化される、この時、
平均化の順序は台数の少ないものから順番におこなわれる
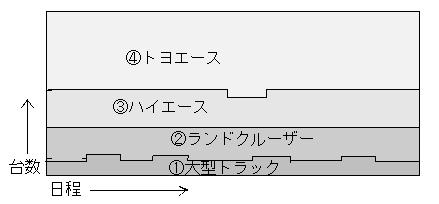
- ハ 車種別の平均化
- 車名別に平均化されると、その枠の中で車種別に平均化される。その時も
台数の少ないものから順番におこなわれる。
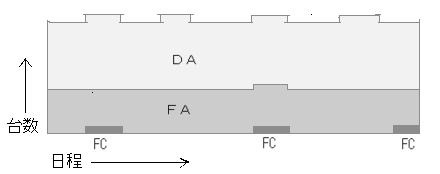
- ニ 車型別の平均化と機能別平均化
- 車種別に平均化されると、その枠の中に各車型を平均に割付けていく。
この割付は、各車型が属する機能の優先順序の高いた車型で台数の少ない
車型から順番に行われる。
主な機能
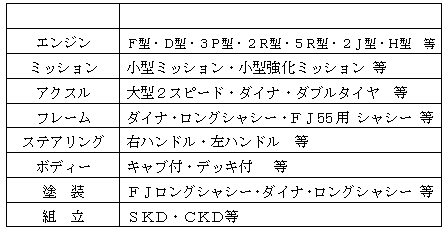
注意:車名別や種別の平均化の結果が、機能別の平均化にもなっているような
車型は、機能を考慮せずに割付が行われる。
以上の平均化は電算機を用いた「日程計画作成システム」で行われている。
又、平均化の条件は現状のものを掲げたが、また充分とはいえないので、
今後も平均化条件の整備につとめていく。
b 組立順序計画
日程計画で与えられた、第1ラインと第2ラインの1日の台数を車型ごとにロット単位に(大型3台、小型5台)に細分し、車型別にロットごとの組立間隔が均等になるように配分する。
又、混合ラインであるので、可能な限り各車型毎に均等化された間隔を
くずさないように組合わせて順序を作り、組立てNOを付与する。
- イ 車名別に平均化する
- ライン別に1日に組まれる総ロット数分の枠をつくり、車名別に間隔が均等
になるよう枠取りがされる。
- ロ KD(輸出の現地組立方式車両)を平均化する
- 社名別に枠取されたら、その車名の内のKD分を等間隔に取る
- ハ 車名別に平均化する
- 組立分とKD分の枠が決まったら、組立分とKD分のそれぞれの枠に車種
を等間隔に割付けていく
- ニ 機能別に平均化する
- 車種別に枠が決まったら、その枠に機能が 等間隔なるように割付られる
- ホ 車型別に平均化する
- 以上により作られた枠に個々の車型を平均的に割りあてていく、この時台数の少
ない車型から順番におこなわれる。
- 以上の平均化は電算機による※COSMICシステムを用いて行われる。
又、平均化条件は現状のものをあげたが、まだ充分とはいえないので、今後も平均化条件の整備に努めていく
※COSMICとはConveryer scheduling & Mamagement Information
Control Systemの略で、組立順序から配車までを電算化した時に
命名したトヨタ用語である。
以上のシステムで下図のように作成される
C 組付順序計画
この計画はエンジン、ミッション、アフスル、フロペラ、ハンドル、フレーム
の各ユニットを組付ける順序として使われている。
これらのユニットは本社工場の第1組立ライン及び第2組立ラインから引取られるほか、元町工場やCKD工場やボデー袈装メーカーにも供給し、パーツも生産している。
この順序は各工程の引取る順序を、引取られる時間の早いものから順番に編成したものである。
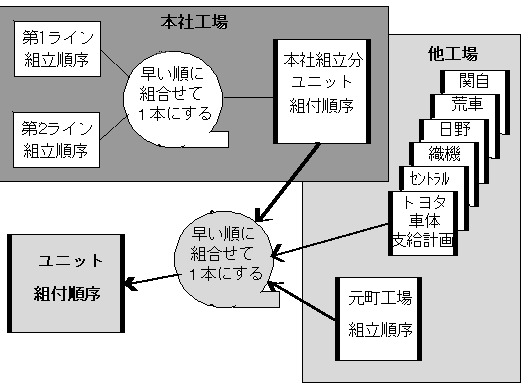
- (イ) 組合せの方法
- ・本社組立の第1ラインと第2ラインの消費速度の早いものから組み合わせる
・次にユニット支給分を等間隔に挿入する
- (ロ) 後工程と生産能力が異なる時の組合せ方法
- 例1 アフスル、プロペラ、ハンドル
この工場は、組立工場(後工程)が1直生産に対して能力の関係から、
現在2直生産をしている
このため、ユニット支給分の生産を組立分の生産後に行うようにしている。
・ユニット支給分を組立分の後ろへ、車型別に等間隔に入れる
例2−F型エンジン
この工場は、現在昼夜2直で生産しているが、組立分及び、ユニット支給分を
間隔に組合わせた原則通りの順序に組合わせている。
この場合、組み立て工場との能力の差は1/2日分の在庫を持つことにより解決
している。
- (ハ) ユニット支給分の生産が主になっている所の組合せ方法
- 例1 R型エンジン
この工場は全生産の25%を本社の組立へ供給し、残り75%は元町工場、関東
自動車、トヨタ車体へ供給しており、又勤務形態も昼夜2交替で生産している
ので、他の工場とは組合わせ方法が異なっている。
・1日の総必要台数を計算し、1/5してロット数を出す
・ロット数だけのエンジン用組付NOを書く
・本社組立向のエンジンを作る時点を決定する(RU用エンジン)
本社組立の始業時の1.5H前から終業時の1.5H前までにラインオフする
ようにし、その範囲内で 間隔にとる
・第2ラインの組立順序表より順序に従って車種を入れていく。
・元町工場のRS及びRTのボデー着工順序より
当日の引取を算出する
・朝、現在のエンジンストアの在庫を調べて当日の生産数を決定する
・ 本社工場向けの後に元町工場向のRS用のエンジンをボデー着工順序に
従って 間隔に入れる
・ 元町向の間に関東自動車向けのRS用エンジンとパーツ用エンジンを
等間隔に入れる
・ 以上で5Rエンジンの割付が完了したら、次に元町向RT43用を空いてい
る所へボデー着工順序に従って、 等間隔に割付ける
・残った所へトヨタ車体向けを割付けて完了する。
d 先行、挽回、増産、減産等の計画変更
計画の変更は、販売よりの要請に早く応じられ、かつ、平均生産ができるように
できるだけ早い時点からおこない、日当たりの負担に大きな差が出ないようにする。
翌月から大幅に増えるような場合は、当月に先行して、ならし生産をする。
また、生産が遅れた場合の挽回計画は、配車計画の許す範囲で、できるだけ平均かして挽回する。
- イ、先行計画
- 1)翌月の内示台数による検討
前月の10日に発行される内示にもとづき、当月の日当たり台数と翌月の日当たり台数を計算し、先行の必要性の要、不要を決定する。
- 2)翌月の確定台数による検討
前月15日に発行される確定計画に基づき1)と同様の検討
- 3)モデル切替計画にもとづく検討
計画が発表される都度、ライン改造期間分の必要台数分先行生産するが、できるだけ日当たり負荷の増加を少なくするよう長期にわたる計画を組む。
- ロ、挽回計画
- 挽回は原則として挽回の可能になった日から月末までを掛け、ならしておこなう。
- ハ、増産、減産計画
- 挽回と同様ならし生産をする。
|
2、生産計画に対するラインの稼動計画
|
---|
翌月の生産計画や、翌旬の日程計画にもとづき、各組立てライン、各組付けラインごとの、車型別生産必要台数を各工場へ示す。
各工場は、この台数を生産するために、必要となる諸対策を講じて、実行に入る時点には、体制が整えられている。
|
3、車両組立、ユニット組付けへの生産指示
|
各ラインへの生産指示は、指令室(コントロール室)がおこなう。
指令室の指示は、工場長命令として、各ラインでは取扱われる。
したがって、指示に反する生産は一切許されない。
また指令室から、最終ラインの車両組立てラインへが、生産順序と生産量が
前工程のユニット組付けラインへは生産順序のみが指示される。
指示は1ロットづつ直前に出すのは、余分なものを作らせないためと指示の変更をなくするためである。
伝達方法は、生産に必要なすべての項目を記入したインターライターでおこなわれている。
- a、車両組立への指示
- 組立て順序表にしたがって1ロット(大型は3台分、小型は5台分)づつインターライターを用いて指示する。
(インターライターとは、写真電送に似た通信機器で、紙テープ上に鉛筆で記入した文字が電気的に送信され、複数の受信機の紙テープ上に放電により文字が再現される装置)
(イ)指示の内容
車型をはじめ特殊な輸出車の仕様に至るまで生産に必要なすべての項目が記入されている。
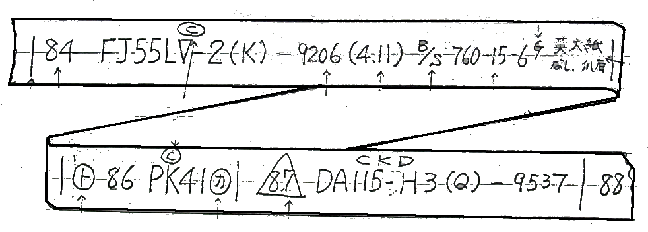
(ロ)指示先
. |
ミッションライン
 | △ ○ |
R型エンジンライン
 | △ ○ |
F型エンジンライン
 | △ ○ |
プロペラライン
 | △ ○ |
ステアリングライン
 | △ ○ |
大型アクスルライン
 | △ ○ |
小型アクスルライン
 | △ ○ |
フレーム塗装ライン
 | △ ○ |
エンジン×ミッションライン
 | △ ○ |
部品トロリーコンベアー フレーム引取り タイヤ引取り
第2総組立てライン

| △
|
部品トロリーコンベアー フレーム引取り ラジエータ組付け タイヤ引取り 第1総組立てライン

| ○ |
|
|
|
(ハ)指示タイミング
車両組立ラインへアップされる15ロット前
(約2.5時間前)
これはリードタイムの一番長いところを基準に定められている。
トロリーコンベアー部品積み込み(10ロット前)+準備作業+α=15ロット
この指示は組立てラインへは生産指示、前工程にはユニットの運搬台車への積み込み指示として使われる。
(ニ)組立て終了指示
毎日、各ライン毎に1日の終了のインターライターNOを知らせる。
この指示は計画に対して±5台以内とし指令室の状況判断で決定される。
伝達方法は、インターライターの指示を四角で囲って知らせる。
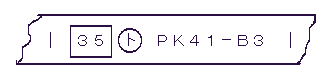
|
b 組付への指示
- 組付順序表に従って1ロット(大型3台、小型5台)づつ
インターライターを用いて指示する。
イ 指示の内容
組立ての場合と同様、組付けに必要なすべての項目を記入する
なお、インターNOは後工程別に文字を分けている
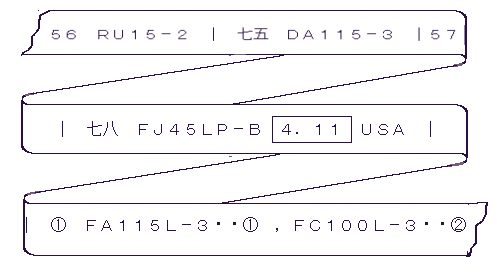
(ロ)指示先
. |
□ | ミッションライン
 |
○ | R型エンジンライン
 |
○ | F型エンジンライン
 |
△ | プロペラライン
 |
△ | ステアリングライン
 |
△ | 大型アクスルライン
 |
△ | 小型アクスルライン
 |
□ | 大型フレームライン
 |
□ | 小型フレームライン
 |
□ | FJフレームライン
 |
□ | ダイナフレームライン
 |
|
|
指令室 |
---|
□ミッション、フレーム用 △=アクスル・プロペラ用 ○=エンジン用
|
|
ハ 指示のタイミング
組立工場のラインアップに対し 40ロット前
約 6 時 間 前
|
これはリードタイムの1番長い所を基準に定められている
大型アクスル工場のブレーキ引取
台車上(10ロット)+塗装ライン(3ロット)+組付ライン(2ロット)
+ブレーキの引取(20ロット)+ アルファ = 40ロット
|
C 仕入れ先への指示
仕入れ先からの部品の納入は、かんばん方式で行こなっているが、1部の
アッセンブリー部品は、自工の組付ライン同様の順序に従った納入がされて
いる
その理由は、物が大きく種類が多いため、各種類ごとに置場を設けて
使われただけ補充する。というかんばん方式だと、置場面積が非常に大きく
なるためである。順序に従った納入をしている仕入先は次の所がある
メーカー | 部品 |
*トヨタ車体 | 全車のキャブ・デッキ |
*豊田自動織機 | 3P・2J・H・Dエンジン |
アイシン精機 | 大型・FJ・ダイナ(フルシンクロ)ミッション、 |
豊性ブレーキ | 全車のブレーキ |
中央精機 | 全車のタイヤ |
トピー工業 | スタウト・大型トラック用タイヤ |
イ 指示の方法
インターライター又は組立順序表による
ロ 指示のタイミング
インター・ライターによる所は自工の組付ラインと同じ組立順序表による所は3日前(5日分づつ)
組立順序表による納入は3日前に5日単位で納入順序が固定してしまう欠点があるので、
かんばん方式か、インターライターによる方式に変えていくよう検討中である。(上図の※印のみ)
|
4、車両組立ラインの稼動と部品の引取り
|
組立ラインは前記した指令室からの指示に従って前工程から、ユニットや部品を引取り、
又トロリーコンベアーや、ラインサイドから部品を供給して、ラインを可動させる
ユニットや部品の引取及びトロリーやラインサイトからの部品の供給については事例2で詳しく説明する。
又ユニットの組付ラインの可動方法についても
事例3で説明する
- イ ラインタクトの決定
- 一日当たりの生産台数から、ラインタクトが決められるラインタクトは、
ラインストップがなければ5〜10分早く1日の計画が達成するように決めら
れる(これを調整時間と呼んでいる)
- ロ ユニットの引取と補充
- 組立ライン(後工程)は指令室の指示した順序に従って1ロットづつ
前工程から引取って来る
前工程の組付けラインは引取られただけ指令室の指示した順序に従って
ユニットを生産し補充しておく
この引取と補充は直接継くのではなく、一定量の台車(在庫)をもって行われ
る
- ハ 部品の供給
- 部品は原則としてトロリーコンベアを使って、指令室から指示された順序
通りに供給される。
ただし、大きなのものや重い物 は直接ラインサイドから供給している。
- ニ 計画の完了
- 一日の最終組立NOは毎日指令室から指示されるが、この計画が完了したら勤
務時間内であってもラインを止める。又完了しない時は完了するまで作業を
継続する
ユニットの引取りと補充
組立ライン | 引取り | ユニット組付けライン |
---|
↓
↓
↓
↓
総
組
立
ラ
イ
ン
↓
↓
↓
↓
|  |  
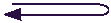
| 

 | 空き台車が無い ラインを止めて、 空き台車が来るまで待つ。 |

  |
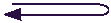
| 

 |
|
 |  
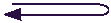
| 

 |
|
 |
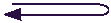
| 

  | 空き台車が多い 管理者は挽回方策を講ずること |
この関係は前工程とその前工程との間も同じである。
|
5、ラインのコントロール5>
|
指司室は生産の指示の他、組立及び組付ラインの可動状況を常に監視し、
ラインストップが発生した場合は即時に要因を把握すると同時に、関係部署へ連絡を取り、対策をさせる。
不具合が発生したら必ずラインを止め、指令室の指示を仰いで生産を再開する。
という原則に従って各ラインは生産をしているので、ラインストップを監視していれば不具合状況を把握できる。
- a ライン可動状況の把握
- イ ライン停止の把握
各ラインの電源と接続させ、ラインが止められると指令室のグラフィック
板に赤ランプが点灯しチャイムが鳴って知らせるようになっている
特に最終工程である組立工場では、9工程に分けられて停止させた部署が
分かるようにしてある。
- ロ 停止回数、停止時間、運転時間の把握
時計と停止スイッチを接続させて、指令室のグラフィック板に停止回数、
停止時間、運転時間の積算が分かるようになっている
- ハ ラインアップ NOの把握
総組立ラインにラインアップする時、電光板によるグラフィック板上に
ラインアップNOが点灯するようになっている
グラフィック盤
|
----------○
----------○
----------○
----------○
----------○
|
----------○
----------○
----------○
----------○
----------○
| |
|
第2ライン
@=A=B=C=D=E=F=G=H
|
|
第1ライン
@=A=B=C=D=E=F=G=H
|
| ライン | 停止 回数
| 停止 時間
| 運転 時間
|
ミッション | 06 | 12 | 258 |
Rエンジン | 00 | 00 | 370 |
Fエンジン | 01 | 01 | 369 |
プロペラ | 02 | 05 | 365 |
大型アクスル | 05 | 15 | 355 |
小型アクスル | 03 | 11 | 359 |
大型フレーム | 06 | 13 | 357 |
小型フレーム | 04 | 08 | 362 |
RUフレーム | 00 | 00 | 370 |
RSフレーム | 01 | 02 | 368 |
FJフレーム | 00 | 00 | 370 |
キャブ儀装 | 01 | 04 | 366 |
組立第1 | 04 | 10 | 360 |
組立第2 | 01 | 07 | 363 |
- b 異常の把握と連絡
- ラインストップがあると、インターホンで異常の状況が指令室に即時連絡が
ある
指令室は要因の内容に関係する前工程(及び管理部署へ)に、次の3段替に
分けて連絡する
- イ 即時連絡
インターホンを利用して発生の都度、関係するラインに連絡し応急処置を
手直しを責任部署にさせる
- ロ 1時間分をまとめて連絡
関係部署の管理者(製造部長)に対して再発防止の対策をするために、
1時間に1度、不具合の状況を放送し、受信側は不在の時にでも分かるよう
にテープ・レコーダーにへ録音するようにしてある
- ハ 1日分をまとめて連絡
ライン状況表に1日分の異常をまとめて翌朝関係部署に配布し、対策を
させる
ライン状況表(3月8日)
ラインストップ | 車種 | 品番 | 責任 | 遅れ | 品質 | 誤品 | 欠品 | 段取 | 内容 |
8:41 | FJ40 | アクスル | 機械 |
|
|
|
|
| アブソーバーブラケット割りピン穴なし |
11:00~11:06 | DA110 | シャックルピン | 組立 | 6 |
|
|
|
| シャックルピン取り付け間違い |
5:00 | DA115 | エンジン | 外注 |
|
|
|
|
| アクセルワイヤ取り付けビスなし |
|
|
|
|
|
|
|
|
|
|
|
|
|
|
|
|
|
|
|
|
|
|
|
|
|
|
|
|
|
|
|
|
|
|
|
|
|
|
|
|
情報体系図
- C.不具合車両の処置
- 不具合車両は、組立工場の最終調整場の前にもうけられた責任部署別の
不具合車両置場に並べ組立工場外には出さない
但し、不具合車両置場が満杯になったらラインを止める
- イ 手直し
不具合車両の手直しは指令室からの連絡により、責任部署が即刻組立工場
へ出向いて行う
- ロ 再発防止
不具合車両の手直しにより、不具合の要因が分かるので即時再発防止の
対策をはかる。
- d その他の異常処理
- イ 設備故障により部品の供給が不可能になった場合、設備・機械 の故障に
より、部品の供給が不可能な事態が発生した場合、関係する車種の生産を
中止する。
この場合指令室は問題発生のラインのみではなく全ラインを中止させる
(挽回の方法は変更計画の項目参照−12ページ頁)
- ロ 外注部品が一時的に欠品するような場合
i)インターライターで指示がされる以前にわかった場合、組付、
組立ライン共に生産を保留する
ii) インターライターで指示された後にわかった場合、不具合車両の
処理と同様、欠品でラインオフさせ、不具合車両の置場に並べる。
但し、不具合車両置場が満杯になったらラインを止める
|