まえがき
|
当社は佐吉翁の自働織機発明以来、自働化についての伝統的な精神が受け継がれてい
る。
この自働化の精神は、不良品は絶対に後工程へ流さないということに基づくものであ
り、佐吉翁の自働織機では、たとえ1本の糸が切れてもその織機は自働的に作業を停
止し、糸が切れたままでは動かなくなっている。
いうならば織機に自働停止装置が付いていて、糸が切れれば、そのとき、その場で
処置ができ良品だけを生産できるようになっている。
不良品をいくら作ったところで材料の浪費であって、仕事をしたこと 働いたこと
にはならない。
即ち働くということは、不良品を造らないことであり、自働停止装置が付いている
ことが自働化である。
これに対して単なる自動化では自動に切替えることによって性能向上分だけ生産性
は向上するが、たとえ規格外の品物ができても機械は動きつづける。
この自働化の考え方を生産活動の面に応用したのがスーパーマーケット方式と呼ばれ
るものである。
これはスーパーマーケット(前工程)が顧客(後工程)にとって、必要とする品物を、
必要なときに必要な数量だけ入手できるマーケットであり、顧客はストックとなるよ
うなものは無理に購入しなくとも(在庫としなくとも)よく、またスーパーマーケッ
トも顧客が望むものを揃えておけばよい、という考えに基づいたものである。
そして、
この考え方を各工程ごとにつぎつぎと繰返すことにより材料取りから総組立工程に至
る一連の作業を少しも停滞させることなく、全体として循環的流れ作業が形成できる
のである。
このスーパーマーケット方式の考え方をさらにすすめ工程管理の改善を目
指したものが「かんばん方式」である。
従来在庫管理の面では発注時点における在庫量がつかめていなかった。
例えば、翌月の生産量が決まるのは当月の中旬であり、その時点では月末の在庫量は
不祥であり、たとえ月末に棚卸しをして在庫量を把握できたとしても、その時には既
に発注を終えた後であるから調整ができない。
また不良品が発生した場合、その補充が迅速に行われていなかった生産活動における
在庫管理は全てのことが計画通り行われたときだけはうまくいくのであって、実際に
計画が計画通り実行されることはほとんどありえない。
そのため在庫過多のものが生
じるしその反面欠品も起りうる。
このような欠陥を無くするために案出されたのがかんばん方式である。
従来の在庫管理を計画にもとずく発注方式とすればかんばん方式は発注時点に在庫量が
把握され計画の変更にも、不良品が発生した場合にも迅速に対応でき適正な処置、
調整等がその都度行いうる実績に基づく発注方式といえる。
この方式では、多すぎるものがないかわりに欠品も起らない。
本来、在庫量の微調整を目的としているこの方式では、非常に大きい変動を起すこと
は最も戒むべきである。
昭和38年以降採用されたかんばん方式は本社工場において逐次ケース バイ ケース
で実施に移され、現在では全面的採用となり、作業量の平均化、在庫量の削減ばかり
でなく設備・機械の自働化、製造方法の合理化、適正な人員配置などにも大きい効果
をあげてきた。
かんばん方式は固定したものではなく、今後時代とともに生産システムの進展にとも
ない更に改善、充実され、すぐれた生産量管理方式として発展していくと思われる。
しかしながら、それを運用する人はいつまでも同じ人ではない。
つまり今後かんばん
方式を運用する人によって解釈が異なったり誤った方向に進んでいく可能性がある。
また、新しくかんばん方式に携わる人には、かんばん方式というものを早く理解させ
る必要性とこれから かんばん方式を実施する場合の参考といった点などから、今日ま
でに実施された本社工場に関連のある事例を系統的に集録し、併せてかんばん方式を
実施するための基本事項を一応整理したみた。
|
1.かんばん方式の原則
|
後工程が前工程へ必要なものを、必要な時に、必要なだけ取りに行き、
前工程は必要最小限の在庫でこれに応じなればならない。
かんばん方式は、現物管理を中心にした生産活動における同調化管理方式であり、通
常の運搬工程を逆にした考え方に基づくものである。
即ち顧客(後工程)がお金(かんばん)をもって、いわゆるスーパーマーケット(前
工程)へ、欲しいもの(必要な部品)を欲しい時(必要な時)に欲しいだけ(必要な
数量)買いに(取りに)行くと考えればよい。
実際に何が、何時、どけだけ欲しいかは顧客(後工程)が最もよく知っているはずで
あり、後工程は必要とするもの以外は引き取らないので後工程にはストックとなるよ
うな余分な在庫はなくなる。
前工程は、後工程があるインターバルで取りにくるので、それまでに必要最少限度の
所定の数量だけ(かんばんによる生産指示分だけ)生産して、所定の置場所に確保し
ておけばよいのであって必要以上のものは生産しないようにしなければならない。
|
2.かんばん方式を実施するための必要事項
|
かんばん方式はサイクルを持ったものである。
このサイクルとは後工程が前工程へ品物を取りに行くことにより生産時
期、生産量、品質等の情報が自働的に前工程に連絡され前工程はこの情
報によって次のものを準備し品物は後工程へ流れるという。
この繰返しをいうのである。
このサイクルが各工程を結び、鎖状に連携し合い生産を同調化し種々な
規制を行っている。
この方式のより良い運営のためには下記事項に留意する必要がある。
- 2−1 生産の継続性
- かんばん方式により生産されるものはある程度継続して生産されるものでなけれ
ばならない。
例えば1個1回だけの個別注文生産の場合は継続性がないのでサイクルが成立し
ない。
- 2−2 生産の平均化
- 工場における各工程での生産は、前後工程の特性に応じ、その工程の能力によっ
てできるだけ平均化することが望ましい。特に最終工程での生産量の平均化は重
要である。
この最終工程での生産の平均化では、1日当りの平均化のみならず、1日分の時
間当りの平均化をはかることが必要である。
最終工程の必要数量に波があると、その前工程に対しては負荷の増減となって現
われ前工程にさかのぼるにつれて、その波を大きく被り各工程を混乱させ、在庫
量に過不足をきたし、目標とする生産計画の達成が不可能になることもありうる。
- 2−3作業工程の合理化・安定化
- 生産能率の向上はムリ・ムラ・ムダをなくすことにあるが、かんばん方式を実施
する際には、まず作業工程が合理化され、安定化していることが望ましい。
そのためには、設備・機械の自働化の工夫をし、機械故障コンベアラインの故障
など突発事故に対する予防保全の体制ができていること
が望ましい。
- 2−4品質の安定
- 「品質を工程でつくり込む」ためには、作業部署では自工程の工程能力を常に把
握し、後工程に対して品質が保証された製品を生産しなければならいない。
自工程での生産が安定していて、初めて出荷可能な品物であって、いくら加工
が完了していても、また所定の数量が確保してあっても品質が保証されていな
ければ所定の在庫とはいえない。
もし、不良品を後工程に送った場合には、その情報はすぐ前工程へフィード
バックされ、前工程の管理、監督者はバカヨケなどの対策を考え、再発防止に
つとめなければならない。
|
3.かんばん方式運営の一般的に方法(約束事項)
|
かんばん方式を円滑に運営していくためには種々な規制が必要であり、
かんばん方式の運営に携わる人は決められた運営のルールを守らねばな
らない。
かんばん方式でいうかんばんとは、何回も使用することのできる指示書
である。
即ち、生産指示書、出庫指示書、運搬(引取)指示書、注文書、
納入指示書などの内容を1枚のかんばんに表示することによって、帳票
や伝票を必要とせず、事務を簡素化し、人員も必要とせず自働的にこれ
らの調整をはたすことを目的とした諸情報伝達のために有機的な働きを
する媒体である。
かんばん方式運営のための一般的な約束事項としては次のものがある。
- 3−1、かんばんの種類と基本的な記載事項
- A)流れ作業の場合
この様式は機械加工部品熱処理部品、組立部品などや応用例
として購入部品に利用している。
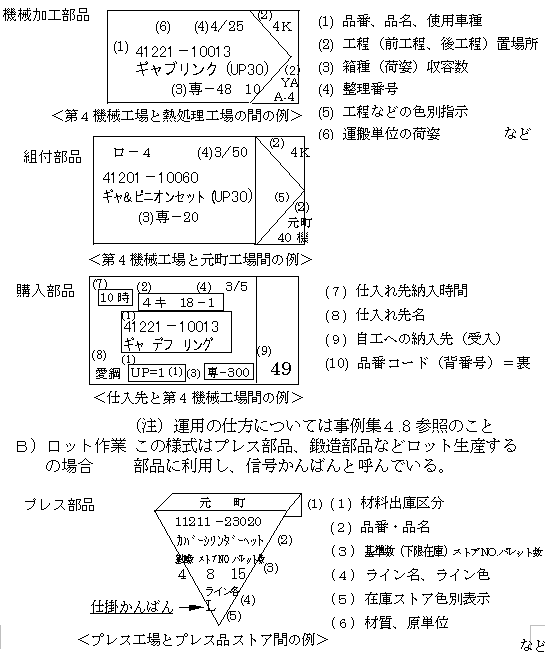
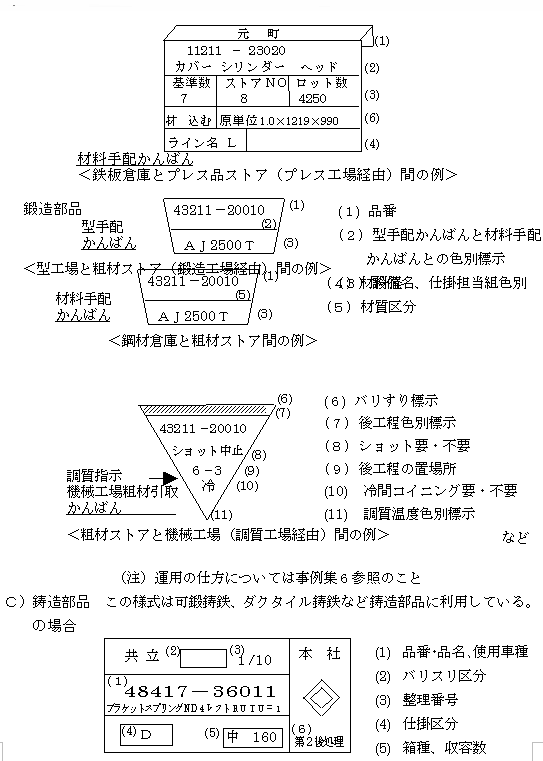
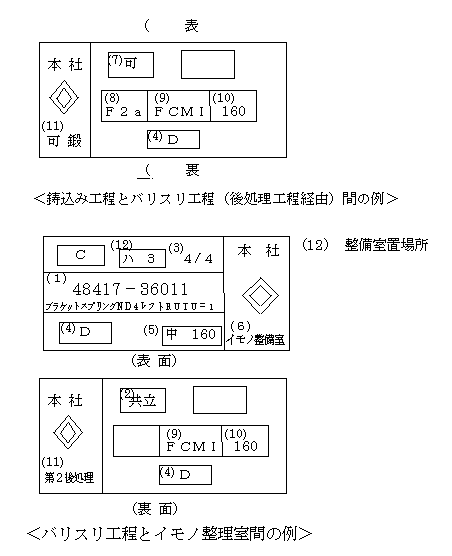
(注)運用の仕方については事例集7参照のこと
- D)少量生産の場合
少量ではあるが毎月あるいは毎日継続して生産される
部品については次のことを考慮してかんばんの様式を決める。
流れ加工部品
(1)必要なもの、必要な量だけ生産するという原則に従って、
1箱の収容数を必要数量に合わせて小さくし、多量生産する
部品のかんばん様式を利用する。
ロット加工部品
(2)信号かんばんの考え方を利用し、手配に必要なリードタイ
ム分だけの在庫になったら次のものを決められた数量だけ生
産する。
この場合のかんばん様式も多量生産する部品の様式
を利用するが、下限在庫量を決めておく必要がある。
- 3−2かんばん枚数の決め方(仕掛数量の規制)
- 3−3部品およびかんばんの置場所の指定
- (1) 部品の置場所(所番地)を明確にする。
※該当部品はそれ以外のところには絶対置かない。
※後工程・前工程とも所定の置場所を決めるときには、
運搬の便利さ、あるいは品質保持ができることを考慮する。
※ 該当部品のかんばんにも後工程・前工程の所番地を明記する。
(2) かんばんポストを所定の位置に設置する。
※ 後工程は部品を使用するときに抜いたかんばんを入れる
かんばんポストを作業員の手近かな所定の位置に設置する。
※ 前工程は後工程が品物を取りに来て空いたかんばんを入れ
る
かんばんポストを設置する。
※ 前工程は、後工程が部品を引き取りに来て、該当部品が無い
時に、つまりその部品が得急状態になっていることを知るた
めに得急品用かんばんポスト(赤ポスト)をも設置する。
- 3−4 かんばんの取扱い方
- (1)後工程では
※ 流れ加工部品では、一般に部品を使用するとき
最初の1個を取り出したとき、かんばんを抜き所定の かんばんポストに入れる。(図1)
A)通常の場合
※ ロット加工部品(プレス品・鍛造品)など信号かんばんを使用す
る部門では、在庫ストアから逐次引き取ってかんばんがかかって
いる箱に手がついたらそのかんばんを前工程行きのかんばんポ
ス
トへ持って行く。(図2)
(2) 運搬工程では
※ 後工程は、かんばんと空箱を持って前工程へ品物を取り行き、
前工程の完成品の置場所で完成品に添付されている前工程の
か
んばんを前工程のかんばんポストに入れ、自工程から持って
来たかんばんを現品に添付する。
※ 後工程が前工程から引き取るときは現品とかんばんとを必ず
セットで、かんばんの指定する運搬単位で引き取りかんばん
に
指定された置場所におく。
(3) 前工程では
※ 前工程はかんばんポストに入れられたかんばん枚数分だけの
現
品を生産し、それ以上は生産してはいけない。1箱分が完成し
ら、かんばんポストからかんばんを取出し必ず1箱毎に1枚づ
つ添付する。
B)異常の場合
(1) 特急品の処置(赤ポストの役割)
※ 後工程が前工程に品物を取りに行ったときに現品がない場合
には、前工程にある所定の特急品用かんばんポスト(赤ポスト)
へかんばんを入れ、前工程に対し該当部品を最優先で仕掛る
ように指示する。
(2) かんばんの紛失の処置
※ “かんばん”はかんばん方式を運用していく上で最も重要なも
のである。
かんばんの紛失は生産活動を停止させるばかりではなく目
標
とする生産達成させ不可能にすることがありうる。 もし、か
ん
ばんが紛失していることが発見されたならば、その責任部署
を明確にし、その部署に対して紛失の再発防止対策を採らせ
た上で、紛失分のかんばんを再発行する。
- 3−5かんばんの役割
- かんばんはある生産工程の量の変動に対して関連する他工程の生産 量をも自律神経的な働きでコントロールしようとするものである
か
ら、各工程間にかんばん方式を採用することより全体として生産量
の同調化をはかることができる。
かんばんのもつ基本的な役割とし
ては次のものがある。
(1) 仕掛についての指示
※ 仕掛の数量・時期・方法(例 焼入温度、サイクルなど)
※ 仕掛の順序・種類(例 流れ加工か、ロット加工か)
(2) 作業状況についての情報提供
※ 後工程の作業の進捗度
※ 仕掛の標準作業の遵守状況
※ 自工程の能力把握
※ 自工程の在庫状況
※ 人員配置の適正度
(3) 運搬についての指示
※ 運搬数量・時期
※ 運搬工程・置場所
※ 運搬具・容器
(4) 異常事態についての情報提供
※ 後工程が必要とする緊急度
※ 仕掛の優先順位
- 3−6 かんばん方式による目で見る管理
- かんばん方式は管理監督者が部下からの報告や紙に書かれた
資料によることなく生産の実態を一目瞭然、目で見て管理できる
ようにしたもので“かんばん”の言葉の由来もここからきている。
目で見る管理の要点は次の通りである。
(1) 標準作業の定着について
作業がかんばんその他の作業標準が示す標準
通り行われているかをたえずチェックして標準通りの
作業が行われるようにする。
(2) ラインストップの対策について
作業者は標準作業ができないときは、ラインを止め
管理・監督者はラインを止められないように処置をとる
(3) 生産工程の改善について
管理・監督者は生産の実態を目で見ることによってムダを
見つけ常に改善を心掛けねばならない。
特に前記ラインストップは生産工程での問題点を顕在化したも
のであるので改善のために100%利用しなければならない。
(注)作業者がラインを止める場合
1. 工程の中で不良が発生したとき。
2. 標準作業が守れないとき。
3. かんばんだけ生産完了したとき
4. 前工程の品質不良を見つけたとき。
5. 欠品するとき。
|
4.かんばん方式と運搬
|
---|
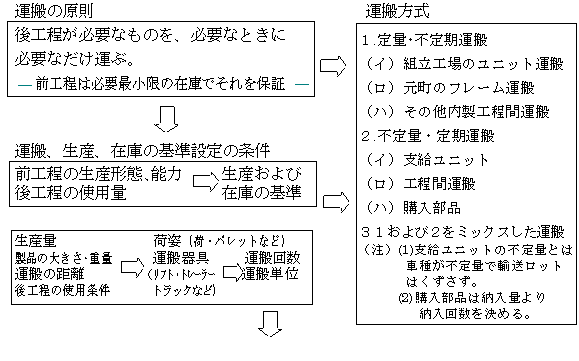
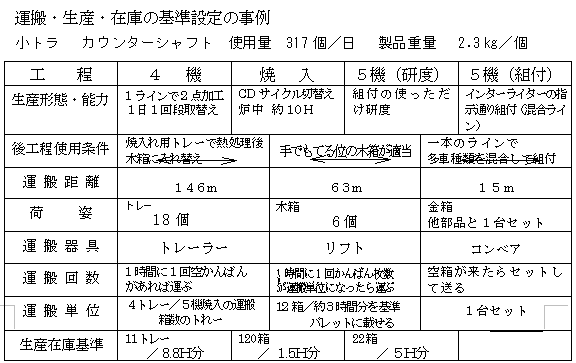
|
5.かんばん方式による同調化
|
各工程間にかんばん方式を採用すれば、各工程は、最終工程である。
総組立工場に同調化したエンドレスチェインで結ばれる。
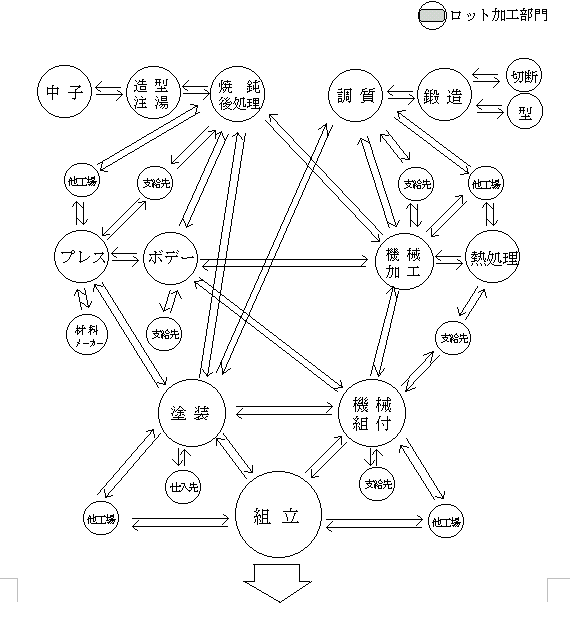
|
事例集
|
---|
この事例集は、本社工場でケースバイケースで実施されてきた。
かんばん方式のありのままをまとめたものであるので改善を要するところ
が随所に見られる。今後これらの箇所を逐次改善し、より充実したかんばん方式
にするために努力して行く所存である。
もし、これら事例集を参考にしてかんばん方式を採用されるときには、この事例集は
完成された姿のかんばん方式について記したものでない、ということを十分に理解し
ていただき、実施する部署に応じた方式を研究されるこてを望みたい。
次へ
|